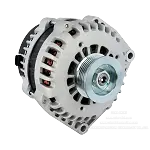
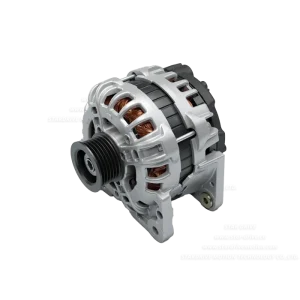
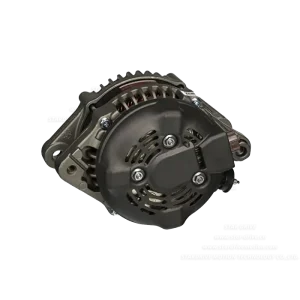
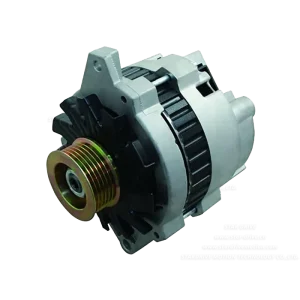
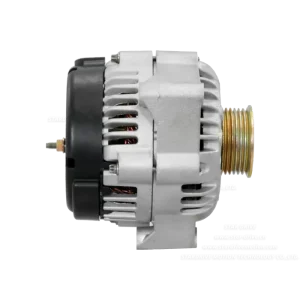
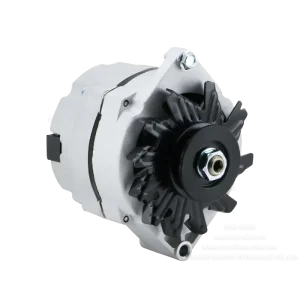
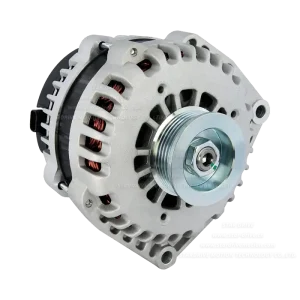
Design: Precision Engineering for Automotive Architecture
(I) Spatial Mastery Across Vehicle Types
- Compact Cars & Sedans: For space-constrained engine bays, we pioneered a “spatial optimization revolution.” Modular integration and millimeter-level refinement of stators, rotors, and regulators enable 30% volume reduction while boosting power generation efficiency by 18%. This lets small compartments house high-performance energy systems.
- Commercial & Heavy-Duty Vehicles: In high-vibration, heavy-load scenarios, our “structural reinforcement protocol” employs aviation-grade aluminum alloy housings, reinforced heat-dissipation ribs, and anti-impact buffers. Self-locking fasteners ensure stability akin to an “energy anchor” under the harshest conditions.
- New Energy Vehicles: Addressing complex energy flows in hybrid/electric models, our “collaborative energy architecture” syncs alternators with drive motors and BMS systems. This enables bidirectional energy flow for efficient power generation and precise braking energy recovery—functioning as an “intelligent energy valve” for next-gen vehicles.
(II) Industrial Design: Performance Meets Aesthetic Harmony
- Anti-Corrosion & Thermal Management: Nano-ceramic coated housings offer 5x enhanced corrosion resistance. Far-infrared coating properties, combined with hollow flow-guiding structures and spiral fins, create an “active cooling loop” that limits high-temperature efficiency loss to ≤5%—surpassing industry benchmarks.
- Customized Aesthetic Integration: Finishes like brushed silver, matte gray, and carbon-fiber texture align with OEM design languages. These elements integrate seamlessly into engine bays, transforming practical components into visual centerpieces.
Performance: Uncompromised Across All Environments
(I) All-Weather Power Generation Dominance
- Extreme Cold Resilience: At -40°C, low-temperature self-activating windings and intelligent pre-excitation technology establish stable voltage within 3 seconds. Below -20°C, efficiency actually increases (due to reduced metal resistance), ensuring full electrical functionality in arctic conditions.
- High-Temperature Stability: In 50°C desert environments, variable-section cooling fans switch to “turbo-cooling mode” at 40°C, increasing airflow by 40%. Dynamic excitation control maintains voltage within ±0.5V, keeping AC systems, lighting, and electronics fully operational.
- High-Altitude Efficiency: Above 4,000 meters, optimized magnetic circuits and intake cooling (for internal combustion engine vehicles) limit power loss to just 8% (vs. 20% industry average). This ensures consistent energy supply during high-altitude climbs and heavy electrical loads.
(II) Core Component Longevity
- Stator Windings: 6N oxygen-free copper with nano-insulation coatings withstands 220°C. After 5,000-hour salt spray testing, insulation resistance remains ≥100MΩ, with a lifespan exceeding 200,000 km—2.5x standard alternators.
- Rotor Assemblies: Hybrid models use rare-earth permanent magnets (1.2T residual flux, ≥1,200kA/m coercivity) with ≤3% decay per decade. ICE rotors feature self-adhesive high-temp enameled wires, eliminating coil looseness and boosting response speed by 30%.
- Rectifier Regulators: Silicon carbide devices with 200kHz switching reduce losses by 40%. AI-driven diagnostics monitor voltage/current/temperature in real time, pre-empting faults and cutting failure rates by 70% versus traditional silicon systems.
Ecology: End-to-End Energy Ecosystem
(I) Full-Spectrum Vehicle Coverage
- New Energy Integration: Custom “energy-sync packages” for EVs/hybrids support 400V/800V platforms and wide-speed power generation. Deep BMS collaboration boosts charging efficiency by 25%, optimizing new energy vehicle energy dynamics.
- Classic Vehicle Restoration: We replicate vintage alternator designs—from 12V mechanical regulators to 24V electronic systems—preserving original “electrical identities” and enabling automotive heritage preservation.
(II) Industry-Wide Energy Empowerment
Through digital pre-assembly and simulation testing, we achieve 99.9% electrical system compatibility with automotive manufacturer platforms. This reduces production debugging cycles by 30%, accelerating new model rollouts. As an “energy accelerator” for automotive manufacturing, we deliver cost savings and efficiency gains from concept to production.
Company Profile
Our business started with humble automotive parts. Building on China’s robust supply chain advantages and our sincere service, we’ve steadily gained trust from global partners while continuously expanding our product range – now covering power window systems, wiper systems, washer pumps, and condenser fan systems.
Most of the time, we provide SKD or CKD to customers.
As motor for window reguator\wiper\washer pump\starter\fan\Alternator.
As rotor assembly/bearing/bushing/motor housing/magnet/carbon brush/commutato/linkage rod/bowden cable/steel wire rope/worm gear/worm wheel/shaft/gear……
In addition, we can also provide complete assembly lines for motors, production equipment for automotive control cables (excluding steel wire rope production equipment), relay assembly lines, stamping equipment, and testing equipment.
Contact Us
Website: www.stardrivemotion.com
Mail: [email protected]